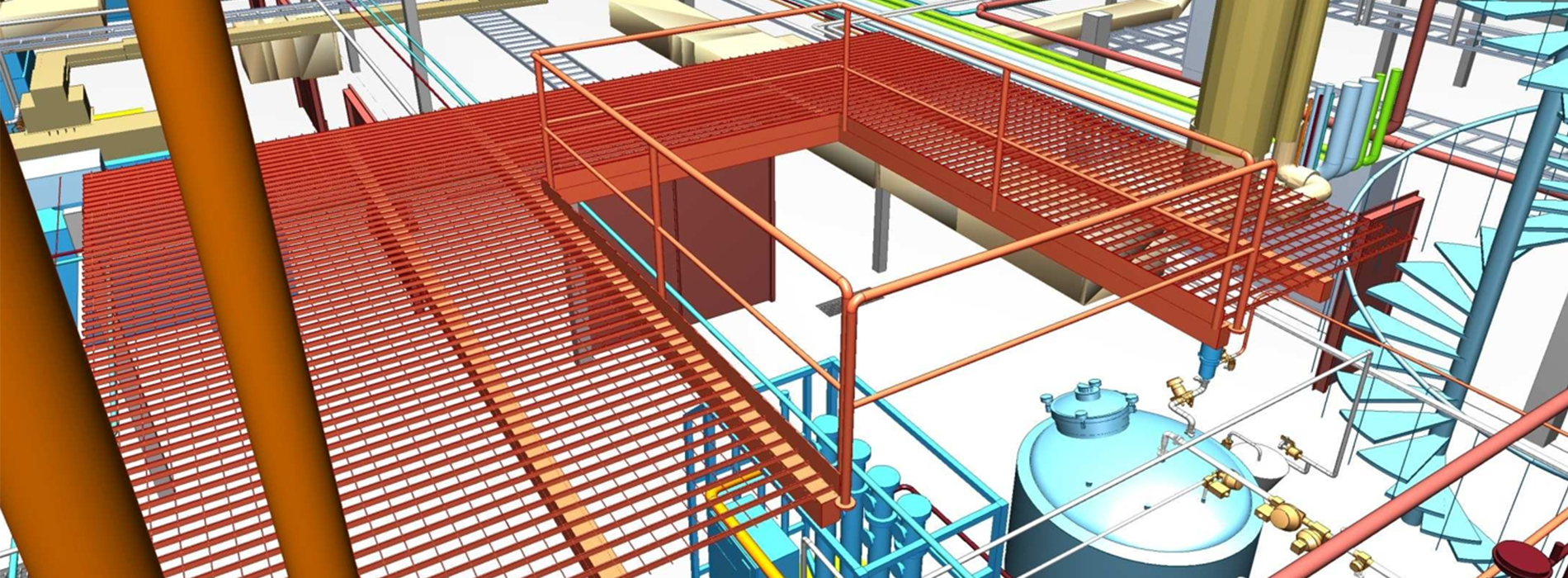
The Injectable Project
The project is to establish a Vaccine formulation, a fill finish facility. This facility is constructed with the aim to export the vaccines under WHO accreditation and also for the domestic requirement.
Total plot area is about 130, 000m2, in southern part of India. Site master planning has been done considering the future expansions of vaccine production with add-on facility of utility block and other infrastructure.
The current investment plan was inclusive of two production blocks for Live Vaccine and for Non Live vaccine, consisting of 5 production lines. Along with entire support function facility like Warehouse , Utility , Electrical , QC, ETP, Landscaping, security cabin, Parking, Administration block etc. since this is Greenfield project.
There are total 5 production lines with various configurations of Fill Finish. The current production area is about 15,000m2 with building structure of G+1 configuration. This is constructed with RCC and partially PEB.
The injections containers are Vials, Ampoules and PFS. Each production line have different capacity of production. There are freezer dryer as well as provision to installed few more in future.
The layout has been design in unidirectional flow of man – material and with long span of column grids so as to have more effective utilization of the useable floor plate. Since this is integrated facility inclusive of live vaccines, the sharing of the common infrastructure along with overall containment philosophy and segregation was very important challenge for the design. The overall segregation strategy for Air, Water, People & Operation was adopted to avoid cross contamination of Live and Non-Live vaccines.
The core production layout has been developed in such a way that complete filling line can be viewed from the outer CNC corridor which will avoid supervisory & other non – productive man power traffic in the sterile section. Further to reduce OPEX which is direct burden on drugs, the classified area in each production block has been optimized with due consideration of maintenance & future replacements, if any.
The provision for the future expansion is planned in such a manner that integrate with common utilities / infrastructure can be done at a very short time interval and with much less additional investment. Which in turn will drastically reduce the loss of production due to down time required during re – qualification & re – validation.
The layout of the entire technical service area is done with due consideration of maintenance, operation, accessibility and future modification within tight investment budgets. Couple of strategies has been adopted to recycle the resources and reduce the utility consumption.
Likewise, A separate disinfectant preparation area has been introduced for sterile production area.
Similarly, special consideration has been given to reduce the travel distance & travel time of various raw material from the warehouse to respective production blocks while making fully utilisation of common facility and infrastructure of the warehouse
Elomatic was sole design and engineering consultant working on this project. The facility has been design under the compliance of local statutory norms. Further during design and implementation phase, CADMATIC™ the proprietary software of Elomatic for design & engineering has been extensively used which ensure very accurate BOQ and a very close coordination of various contractor and vendors.
This project has been designed & constructed under the leadership of Elomatic which is State – of – Art facility and which is full hearted appreciated by regulatory bodies as well as local governing bodies. The project was successfully completed in record time schedule and within the tight investment budget.
The Board at the client place has appreciated the restless efforts & technical leadership demonstrated Elomatic.